The History of Blacksmithing
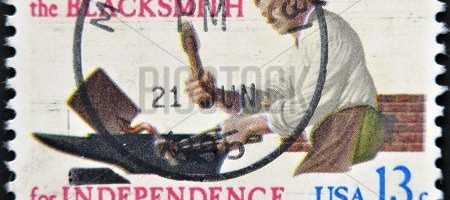
The History of Blacksmithing
Blacksmithing began with the Iron Age, when primitive man first began making tools from iron. The Iron Age began when some primitive person noticed that a certain type of rock yielded iron when heated by the coals of a very hot campfire. In short, we can say that blacksmithing, the art of crafting that crude metal into a usable implement, has been around for a long, long time.
And for a long time after that, blacksmithing remained a crude art. It took three thousand years for man to learn the science of metallurgy. Long after man made the first simple tools–the first spear or arrow tips–the craft would require hundreds more years before blacksmiths understood the magnetic properties of iron. The first compass used a forged iron needle that floated in a round vial. This was a great discovery. By forging the needle as perfectly as he could, the blacksmith aligned the molecules in the iron and that is why north is north and south is south. From that point on, sailors could travel without need of stars nor sun to plot their courses around the globe.
As to where and when blacksmithing evolved depended on fuel and iron ore. Early on, man discovered that small meteorites contain iron. Iron is also present in nodules of bog ore, small lumps of iron created by bacterial life in swampy areas. Iron ore is also present in rock strata that have a red color, and the deeper the red hue, the higher the iron content.
Charcoal was the primary fuel for an iron furnace. Beginning in the 18th century, ironworks began converting coal to coke. In addition to charcoal and iron ore, a flux agent (limestone or dolomite) is also needed to smelt iron ore.
It became a quest to find the rock strata that gave up its iron with the least amount of work. Given the weight of the ore and the large amounts of fuel needed to smelt the ore, the earliest ironworks were located in areas where iron, flux, and fuel were ample and in proximity to each other. The ironworks also had to be in an area where transporting the finished iron ingots was practical. In early times, that often meant being near a navigable waterway.
Early iron smelters called “bloomeries” were small furnaces built from rocks that could withstand repeated heating. These furnaces looked like beehives with a vent in the top and an entry portal on the side. To create the high heat needed to smelt iron, smiths pumped air from a bellows through the tuyere (nozzle). The furnace was filled with charcoal and iron ore and the charcoal was then set afire. When the temperature rises above 2,800 deg.F, the iron flows from the ore and forms blooms.
Using large tongs, the blooms of iron were pulled from the oven and placed on an anvil. A striker would then hammer the lumpy piece of raw iron into a flat, rectangular bar. The bar would be folded over and hammered again. This process would continue several more times until most impurities had been driven from the ingot. The finished ingot, bearing the layers of the folding process, was called “wrought iron”.
Wrought Iron had a very low carbon content making it much weaker than steel. But wrought iron was very malleable, a property that lends itself to forging and forge welding. A forge weld is a homogeneous weld that aligns and bonds the molecules of the iron as if it were one piece; hence, a seamless bond if done properly. The layers, or laminations, in the wrought iron also gave it more strength than if it were only a single layer. These qualities of wrought iron gave blacksmiths a perfect metal for making gun barrels. A brief understanding of history should tell you that blacksmiths have always been part of the “military-industrial complex”.
Cast Iron differs from wrought iron. Cast iron is iron that is heated to a liquid state and then poured into a mold. The mold is lined with sand and a small mix of clay to hold the sand in shape. A finished casting has a rough surface because of the sand texture it was poured against. Oftentimes, people mistake cast metal for forged metal but a quick examination of the surface will differentiate the two. Many ornamental iron fences, window and door grills, and other decorative ironwork pieces are cast. Cast iron is poured at a foundry, not a blacksmith shop. Cast iron cannot be heated and re-shaped, or (conventionally) welded. Wrought iron can be reworked forever. Cast iron contains more carbon than wrought iron. As it cools, the iron crystallizes and tends to be brittle.
To fuel the smelter or the forge, wood is converted to charcoal, or coal is converted to coke. Destructive distillation, the process name, means burning the raw fuel with limited oxygen. The impurities are burned off leaving nearly pure carbon which is what you know as charcoal or coke. (The charcoal in your barbecue grill has been adulterated for cooking purposes and will not fuel a forge.) To get the charcoal or coke to burn even hotter, air is forced to the fire. In early times, this was done with a bellows pumping air through a pipe into the hearth or forge. The bellows was pumped either by hand or by a water wheel. The result is a very hot, sustained fire.
Learning about charcoal making and learning about a forced-draft fire made the iron age possible. This was the only way to generate enough heat to smelt iron ore.
As coke-making evolved, man learned that the smoky by-products from coal could be condensed and made into different chemical products. Tar, a road building and roofing product, was made this way as were the first chemical dyes. The first raincoat, called a MacIntosh for its creator, was made in Scotland from canvas cloth covered with a coal tar. Our modern chemical industry began with the coke-making process and that was before oil was pumped from the earth.
At one time, charcoal plants also made chemicals but never to the extent that coke plants did. However, methanol is still called “wood alcohol” by many even though it has been a century or more since methanol was made from wood in any quantity.
As this whole iron industry evolved over time, blacksmithing became an umbrella for several specialties. The blacksmith who made suits of armor was an Armorer. The blacksmith who made knives and swords was a Bladesmith. The blacksmith who made locks was a Locksmith. The blacksmith who made gun barrels and triggers was a Gunsmith. The blacksmith who shod horses was a Farrier. Generally, the blacksmith we remember was a man who possessed all of these skills. Call him the “village smithy”. The differentiation lies mainly in that his shop was not geared for making one particular type of product.
In colonial America, the village blacksmith was called upon to do many things. I have heard it said that some blacksmiths pulled teeth, no doubt meaning that a village without a dentist had to rely on the one man with a set of pliers! [See note 1 below.] Let’s just leave it at this. Making an axe or a knife or a fireplace crane or a set of door hinges or a handful of nails was what the village smithy did. His shop was the local hardware store. He could also repair a log chain or put rims on the wagon wheels or fix the axe that got chipped when it hit a rock. Whether the village needed swords or plowshares, the blacksmith made them. For without the blacksmith, the village could not survive.
Leif Ericson, Christopher Columbus and all the other European discoverers brought blacksmiths on their travels to the New World. Had they not done so, the trip could have been one way and possibly ended somewhere in the mid-Atlantic. From then on, every ounce of iron had to be transported here until an iron industry could be developed. And that took a century or so.
Over the centuries, blacksmiths experimented with iron and other metals in their search for a more durable metal. The hardening and tempering processes were invented. They also learned different ways to modify the carbon content of the iron, thus allowing iron to be used for even more purposes. A blacksmith needed so many different tools with differing hardness that he was always tinkering with ways to improve the properties of available iron. Punches needed to be hard but not brittle. Knives needed to hold an edge but not be so hard that it took a long time to sharpen them. A blacksmith had to have several files in his tool chest. All of this led to the development of the tool steels and alloyed metals that we have today.
By 1,500 BC, the European Hittites had conquered present-day Syria and began smelting iron. They were the first known civilization to make wrought iron. Centuries later, Damascus would lend its name to pattern-welded iron. Damascus patterns are unlimited in their variety and beauty. Pattern-welded iron/steel is very strong and durable, which is why it is used in making swords and knives.
Blacksmithing in America prospered until the Industrial Age made small enterprises all but obsolete. By the late 1800’s, the railroads had linked the country and hardware was manufactured at plants and sold in hardware stores. Then came the automobile, and the last days of the wagon makers ended by World War I. The Studebaker family, blacksmiths first known for their Conestoga wagons, were able to make the transition to the automobile. Even so, Emmert Studebaker never lost his love of the forge and anvil. He was an accomplished blacksmith and sponsored the Quad State Roundup at Tipp City, OH until his death in the late 1990’s.
The blacksmith survived but only as a specialty. A good example is the Samuel Yellin Ironworks in Philadelphia. The Industrial Age created so much wealth that the government started the Federal Reserve banking system. Some of Yellin’s early commissions were to make the iron grills for the windows of the Federal Reserve banks. Other blacksmiths prospered by making intricate ironwork (such as staircases) for the mansions of the new millionaires in the 1920s. But most of the rest were relegated to the maintenance departments in the plants that replaced them.
The Great Depression and World War II all but ended the renaissance in decorative ironwork. The blacksmith that Longfellow praised in his poem became about as extinct as the chestnut tree he worked under. Only in the last 40 years has blacksmithing made a comeback. The art today is different, however. It exists at theme parks, restoration villages, craft fairs and craft shops, and yes, in the mansions of new millionaires. But today’s blacksmith is more of an interpreter of the past, in essence – an artist, rather than the real item. Today’s blacksmith uses many of the same techniques and methods but the electric drill, electric grinder, power hammer, ox-acetylene torch, and electric blower for the forge greatly reduce the physical effort in modern blacksmith shops.
Through associations such as ours, the art and the knowledge of blacksmithing is being passed on. In large part, blacksmith associations were started because people remembered a grandfather who had an anvil at his farm and they wanted to learn more about the art. What was a necessity to great-grandpa is really a leisure activity to most of us today. The public has responded to this resurgence by buying the wares of modern blacksmiths, but the trend has been towards artistic work rather than common tools or goods. The new millionaires may have their spiral staircases, but the average family is just as proud of its garden gate, chandelier, wrought iron bed, or fireplace screen.
Another major reason for the resurgence in this art is Francis Whitaker. He began his career at the Yellin Ironworks but left there to go into business for himself. Despite the hard times of the 1930’s, he managed to prosper by securing commissions around the country. When he considered retirement about 1970, he looked around and realized he was “the last man standing.” From that realization until his death in 1999, he toured the country promoting and teaching blacksmithing to generations who knew little of the art.
I doubt that the blacksmith of olden times would ever guess that the iron rod on my kitchen wall holds a roll of paper towels. In fact, he’d probably have something derisive to say about paper towels since he’d reuse every scrap of iron that he came across. But those are the ages, his and ours. We do live in a different age and the blacksmith of old doesn’t figure into the equation anymore. After all, who buys a magnetic compass needle when a GPS satellite can pinpoint one’s location at the touch of a button?
We do need to appreciate the man who really built our modern world, the blacksmith. In peacetime and in wartime, the blacksmith was called on to do many tasks. Ben Franklin, in his Poor Richard’s Almanac, wrote, “For want of a nail, the shoe was lost. For want of a shoe, the horse was lost. For want of a horse, the rider was lost…”. In “The Village Blacksmith”, Henry Wadsworth Longfellow praises the blacksmith: ” His brow is wet with honest sweat, He earns whate’er he can, And looks the whole world in the face, For he owes not any man.”
Such are the sentiments of an age gone by. For who in modern society could qualify now for Longfellow’s praise? I doubt we’ll ever hear such a romantic overture about lawyers, consultants, engineers, computer programmers, civil servants, doctors, or for that matter, anyone else.
For the entire article and more details the history of iron and blacksmithing click [ HERE ] for the Appalachian Blacksmith Association’s website & info!